In computer numerical control (CNC) machining, whether you're crafting a single prototype or scaling to large production, the primary goal often remains to reduce manufacturing costs. Design decisions play a crucial role in helping keep these costs down. By following certain Design for Machinability (DFM) rules, you can manufacture affordable parts while still adhering to functional design requirements.
This article presents valuable tips to help optimize your design for cost savings. We begin by looking at what drives costs up in CNC machining, followed by comprehensive guidelines that offer proven strategies to reduce your project's overall cost.
How Much Does CNC Machining Cost?
The cost of CNC-machined parts is determined by several factors:
1. Machining Time:
The longer the machining time, the higher the cost. Machining time is often the main driver of cost in CNC, particularly for large-scale productions where design errors can undermine economies of scale.
2. Start-Up Costs:
These are related to CAD file preparation and process planning and are particularly significant for smaller volumes. Fortunately, they are fixed costs, meaning you can reduce the unit price for larger orders due to economies of scale.
3. Other Manufacturing Costs:
Special tooling, closer quality control, and additional steps at lower machining speeds are necessary for features that are harder to machine (e.g., thin walls), increasing both time and cost.
4. Material Cost:
The cost of the bulk material and how easily it can be machined greatly affect the overall cost. By optimizing your design and carefully considering the material, you can lower costs.
Understanding what drives CNC machining costs can help in optimizing designs to lower the budget.
How to Reduce CNC Machining Cost
1. Add a Radius in Internal Vertical Edges
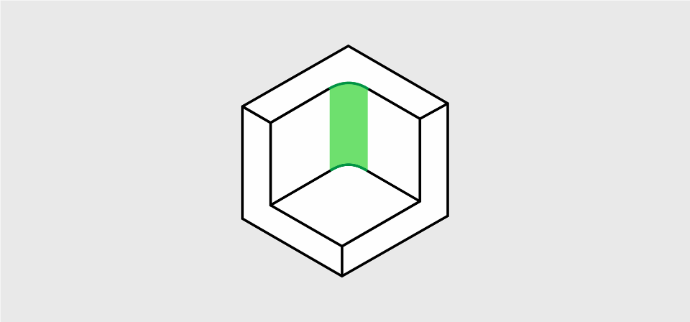
All CNC milling tools are cylindrical, which means they naturally create a radius when cutting the edge of a pocket. This necessitates smaller tools for more detailed cuts, which require multiple passes at slower speeds, driving up machining time and cost.
To minimize cost, it's recommended to add a radius of at least one-third of the cavity’s depth, ideally making the radius larger. If you use the same radius for all internal edges, you can avoid unnecessary tool changes, thus saving time. On the floor of the cavity, use a smaller radius (e.g., 0.5 or 1mm) or no radius at all. A radius slightly larger than the tool used for cutting reduces tool load and cuts costs, allowing for faster speeds.
For sharp corners, consider using undercuts to the cavity instead of reducing the radius.
2. Limit Cavity Depths:
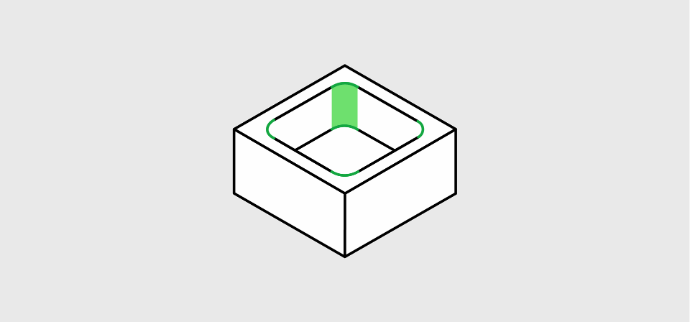
Machining deep cavities can dramatically increase the cost because a significant amount of material must be removed, which is both time-consuming and wasteful. CNC tools have a limited cutting length, and they perform best when cutting cavities no deeper than two to three times their diameter. Deeper cavities often require special tooling or multi-axis CNC systems, both of which increase costs.
To minimize costs, limit cavity depths to four times the cavity's length. This reduces the need for specialized tools and additional processes.
3. Increase Wall Thickness:

Thicker walls are more stable and less expensive to machine than thinner walls. Thin features are more prone to vibrations, which can make machining them accurately difficult, leading to longer machining times and higher costs.
To minimize the cost, ensure wall thickness is greater than 0.8mm for metal parts, and for plastics, aim for walls thicker than 1.5mm.
Thin walls close to the edge of a part can be problematic when holes are placed nearby. Keep this in mind while designing.
4. Keep Threads Short:
Longer threads require special tooling, and if they exceed 1.5 times the hole diameter, they don’t provide additional strength.
To minimize cost, design threads with a maximum length of up to three times the hole diameter. Additionally, for threads in blind holes, ensure the unthreaded section at the hole's bottom is at least half the hole's diameter.
5. Stick to Standard Hole Sizes:
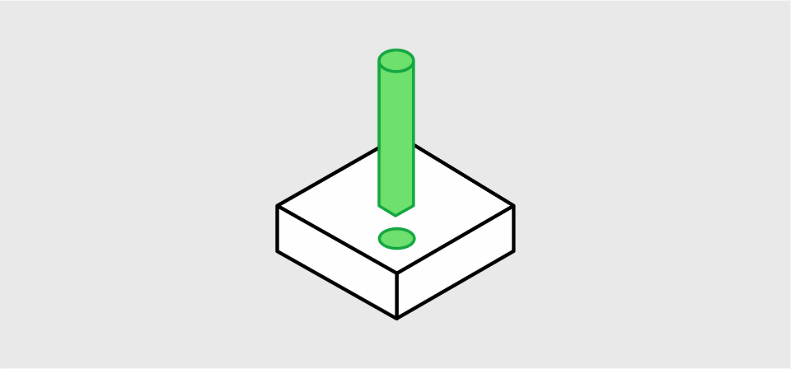
CNC machining can efficiently and accurately machine holes using standard drill bits. For non-standard sizes, additional steps are required, which increase costs. Stick to standard hole sizes and, if possible, use through holes rather than blind holes, as they are easier to machine.
To minimize cost, design holes with diameters that are increments of 0.1mm for sizes up to 10mm, and use an increment of 0.5mm for those above 10mm.
6. Only Specify Tolerances When Necessary:
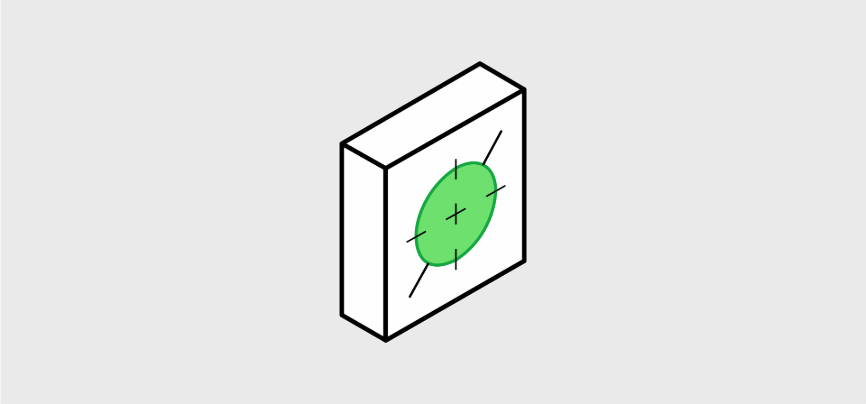
Defining tight tolerances raises the cost of machining. Parts that don’t require specific tolerances can be produced more affordably using standard tolerances (±0.125mm or better).
To minimize cost, specify tighter tolerances only when absolutely necessary.
A good approach is to define a single datum (e.g., the cross-section of two edges) as a reference for all dimensions with tolerances.
Pro Tip: Use Geometric Dimensioning and Tolerancing (GD&T) to reduce costs as it often allows for looser tolerances while maintaining part functionality.
7. Minimize Machine Setups:
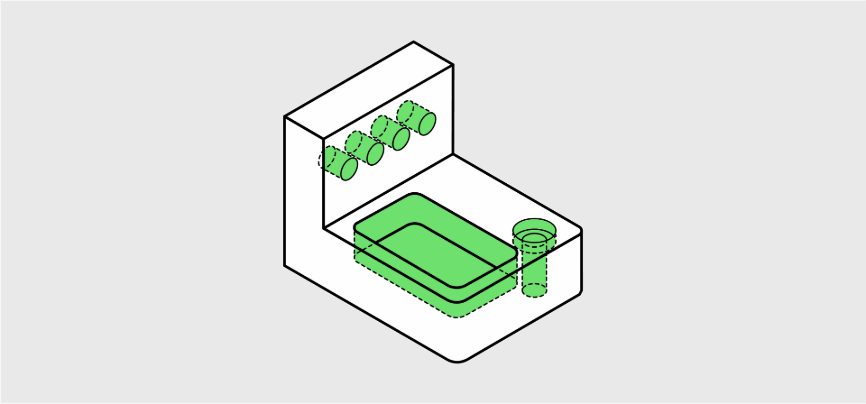
Parts requiring multiple setups increase machining time and cost. Ideally, design parts to be machined in a single setup. If this isn’t possible, and to minimize cost, consider separating the part into multiple geometries that can be machined in a single setup and assembled later. This approach helps reduce the need for additional machine setups and custom fixtures.
8. Avoid Small Features with High Aspect Ratios:
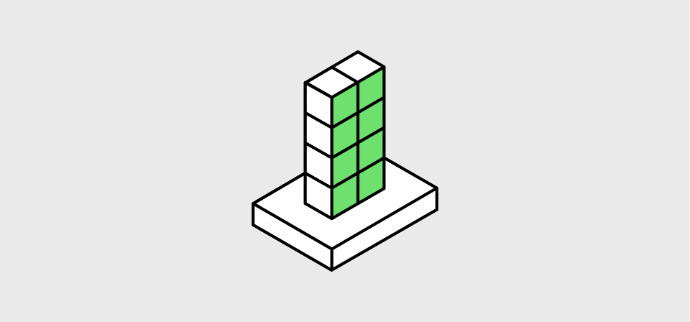
Small features with a high width-to-height ratio are prone to vibrations and difficult to machine accurately.
To minimize machining difficulties and cost, design features with a width-to-height aspect ratio less than four, or add bracing to improve the stiffness of smaller features.
9. Remove Text or Lettering:
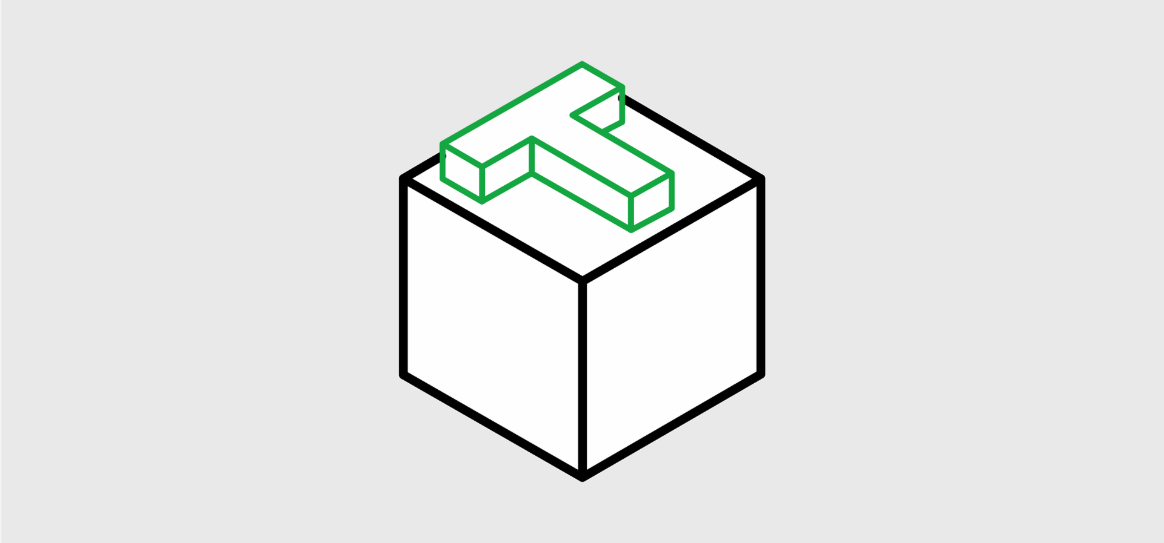
Text or lettering on CNC parts can increase machining time, adding unnecessary costs.
To minimize cost, instead of engraving text, consider surface finishes like silk screening or painting. If text is necessary, opt for engraved lettering and keep the font simple and legible, using size 20 sans serif fonts like Arial or Verdana.
10. Consider Material Machinability:
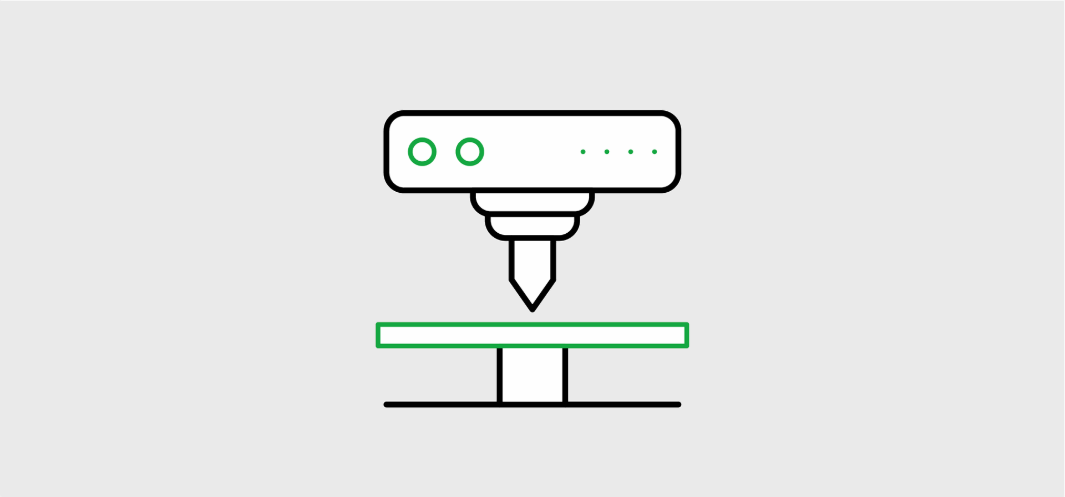
The machinability of a material plays a significant role in CNC machining costs.
To minimize the cost and time, use more ductile materials, such as C360 brass and aluminum alloys, which are easier to machine.
In contrast, materials like stainless steel take much longer to machine. Plastics such as POM (Derlin) and ABS are easier to machine, while others like PEEK are more difficult and expensive to work with.
11. Choose Cost-Effective Materials:
The price of bulk material can greatly affect CNC costs. Aluminum 6061 is an affordable material with excellent machinability, making it a great choice for prototypes. Stainless steel and C360 brass cost more, but their better machinability can be cost-effective for larger orders. Plastics such as ABS and POM are similarly priced to aluminum 6061, but they may incur higher machining costs.
To minimize cost, choose materials with lower bulk prices, especially for small-volume orders.
12. Limit Surface Finishes:
While surface finishes improve the part's appearance and resistance to harsh conditions, they also increase machining costs. Requesting multiple surface finishes can drive costs even higher.
To minimize the cost, limit surface finishes to “as machined” unless multiple finishes are absolutely necessary.
Best Practices for Lowering CNC Costs
In conclusion, keeping your CNC machining simple is key to lowering costs. Complex geometries, special tooling, and custom fixtures all drive up the price. Before submitting your design for quoting, ask yourself the following questions:
- Have I optimized my design using DFM guidelines?
- Can I remove or simplify features while retaining full functionality?
- Can the design be separated into multiple parts for easier machining and assembly?
- Is there a material that’s more cost-effective or easier to machine for my requirements?
The Present & Future of CNC Machining
As CNC machining continues to evolve, recent advances in tooling and CNC systems allow for greater efficiency and versatility. With a deeper understanding of design for manufacturability, you can optimize your design to reduce costs, regardless of the CNC system in use.
Need CNC machining for your project? Get a fast and hassle-free quote using our Instant Quote feature. Simply submit your requirements, and we'll provide a quick estimate. For any inquiries or assistance, feel free to reach out to us—we’re here to help!
CTA: Get a Quote
Contact Us:
Email: [email protected]
Phone: (+91) 9898412126