Metal bending and welding are two common techniques used for metal fabrication. Every technique has its applications, advantages, and limitations. Project managers and engineers should know which of these two techniques will work best for their requirements. This blog explains the difference between sheet metal bending and welding for your project.
What is Metal Bending?
Metal bending is a manufacturing process for deforming either metal sheets or rods into different shapes without breaking material. It is useful for making geometrically consistent parts. The two common types of metal bending are air bending and bottom bending.
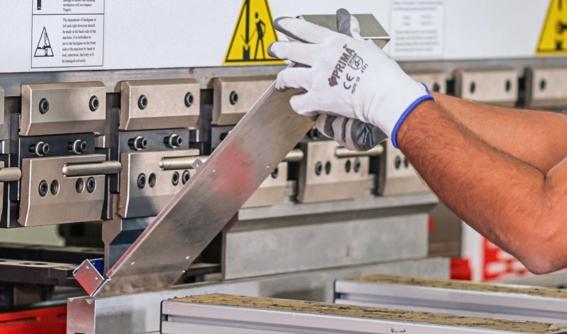
Advantages of metal bending
1. Preserve Material Strength
Metal bending does not use heat and the metal retains its original strength and structural strength.
2. Cost- Effective
It is cost-effective as it requires less labor and fewer tools or materials
3. Smooth and clean look
Metal bending gives a seamless appearance without any visible joints or beams.
4. Increase structural strength
Adding bends in the metal increases its durability and makes it stronger.
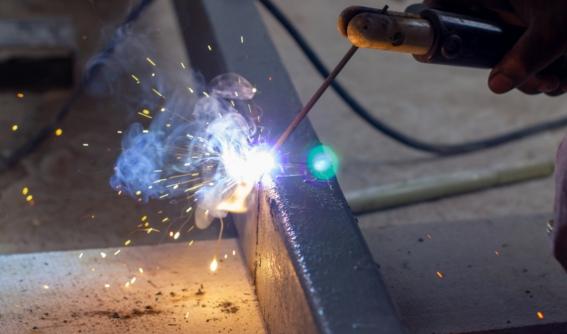
What is Metal Welding?
Welding is a technique of fabrication through which two or more pieces of metal are fused into one by melting the ends. When it cools down, it forms a joint. There are many types of metal welding, including sheet metal welding, MIG ( Metal Inert Gas) Welding, and TIG (Tungsten Inert Gas) Welding.
Advantages of metal welding
1. Material Compatibility
Welding is highly versatile and is used for joining materials like steel, aluminum, and iron.
2. Durable
Welding joints offer more strength and robustness than bent metal.
3. Complex Shapes
Welding provides detailed and intricate designs that bending cannot achieve.
4. Seamless Integration
Welded components blend smoothly, which results in a uniform and professional finish without visible seams.
Choosing Between Metal Bending and Welding
These are some factors one must remember before going for metal bending or metal welding:
1. Project Requirements
Strong Joints: Industrial construction projects or large machines require high structural integrity, which is possible by welded joints. Metal welding is done to withstand heavy loads and stresses.
Complex Shapes: If your project has complicated designs or geometries, metal bending would be the best choice. With the help of only one raw material, metal bending helps the object transform into complicated shapes. It reduces the number of joints as well as potential failure points.
2. Material Type and Thickness
Material Suitability: Materials like aluminium and certain steels have high ductility. Due to this feature, it can be bent easily. Hard materials are tough to bend and may need welding.
Thickness Concern: The thickness of the material has an important role. Thicker materials might have to be welded for sufficient joint integrity, whereas thinner sheet metal can usually be bent without breaking.
3. Cost Considerations
Initial Cost: The initial process of sheet metal bending is not costly. This is because it requires minimum tools and setup. This makes it a good choice for projects that are on a budget or need fast prototyping.
Labour Costs: Welding costs are closely tied to labour efficiency and technique. Skilled welders can save time and costs by ensuring strong, durable joints in the final product, which reduces the likelihood of future repairs.
4. Production Volume
Low to Medium Production Runs: Bending involves low set-up costs and short lead time as compared to other processes. Thus it is better suited for companies requiring lower production volumes. It allows design changes at a reduced cost.
High-Volume Production: If high-volume productions are carried out on a large scale, the welding process is used for efficiency. The automated welding processes save a lot of labour and boost production rates.
5. Lead Time
Turnaround Times: If your project has tight deadlines, consider which method offers quicker turnaround times based on your specific requirements and available resources. Bending processes can often be completed faster than welding setups, especially if tools are readily available.
Project Timeline Flexibility: If you have enough time, you might choose welding for its strength benefits. It may require longer lead times due to setup and finishing processes.
Conclusion
Bending and welding are important techniques for sheet metal fabrication. Each of them has its advantages depending on the requirements of a project. Knowing the special strengths and limitations of both helps in making a lucid choice that best fits individual objectives.
Choose Mech Power for reliable sheet metal fabrication. With advanced bending for complex shapes and high-precision welding for strong, seamless joints, we deliver cost-effective, durable solutions tailored to your project needs. Click here to learn more about Sheet Metal Fabrication service.